An Overview of Weld Overlay or Cladding: How It Works, Advantages, and Applications
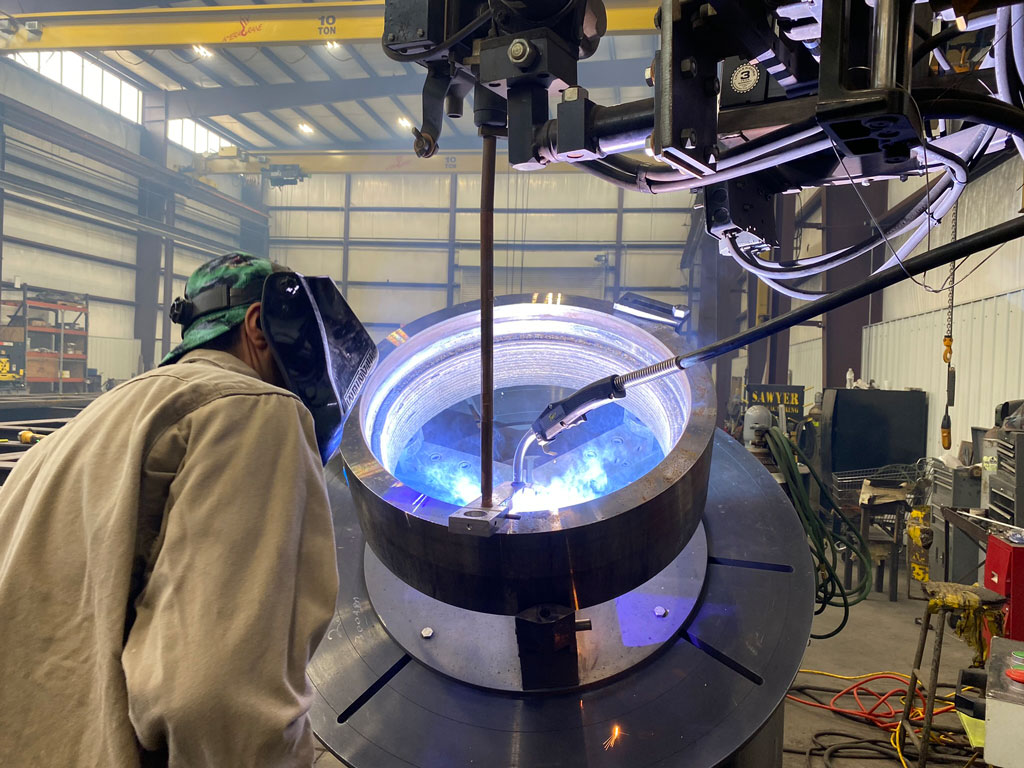
Weld overlay is one of the many metal fabrication services we use consistently here at Sawyer Fabrication. Commonly referred to as weld cladding (and sometimes mistakenly equated with hardfacing), overlay welding melts one type of metal over top of another to create a robust protective layer, or a new surface layer with unique material properties. The process is ideal for increasing corrosion resistance, wear resistance, or enhancing other mechanical properties of industrial components generally used in harsh operational conditions.
Let’s take a closer look at exactly what goes into the weld overlay process.
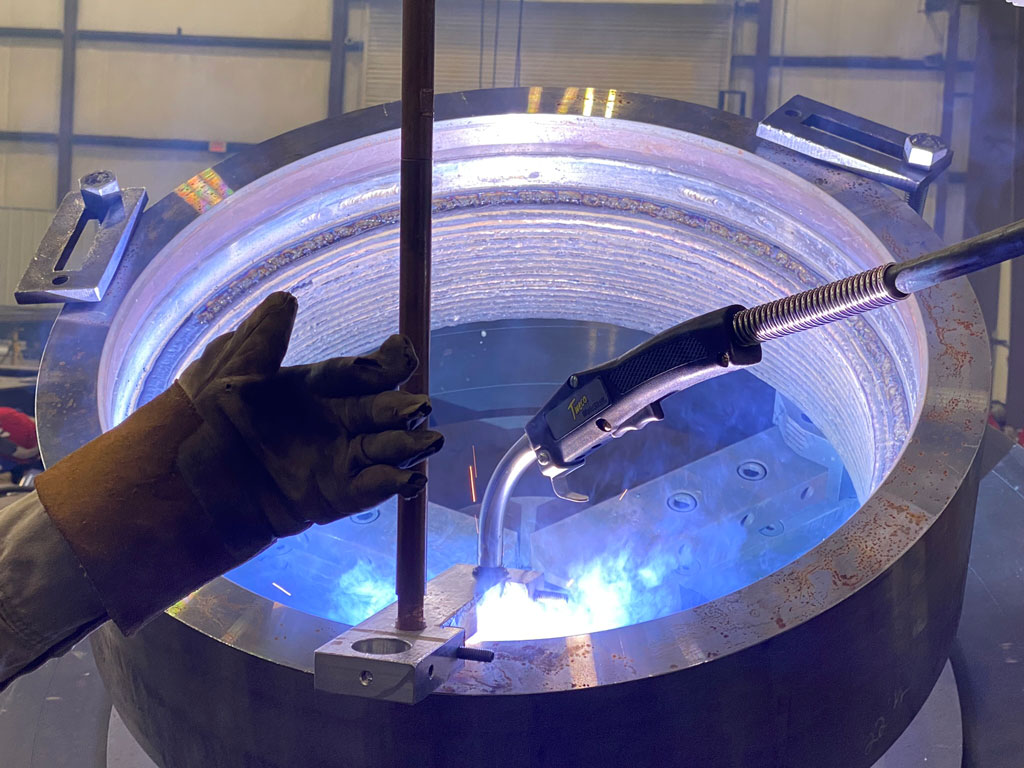
The Basic Anatomy of a Weld Overlay:
Base Material (Substrate)
As the name suggests, the base material is the original component or workpiece that we need to enhance. This can be any type of metal that we typically use in our custom welding services.
Of course, the choice of base material depends on the end product’s application requirements – most commonly strength, toughness, and chemical reactivity. However, the best metal to achieve these mechanical properties isn’t necessarily the best metal in terms of surface properties. Enter weld overlays.
Overlay Material
The weld overlay material is a specialized alloy or metal coating that we select based on the specific performance needs and operational conditions of the end product. For example, common overlay materials include corrosion-resistant alloys, wear-resistant alloys, and materials with specific thermal or electrical properties.
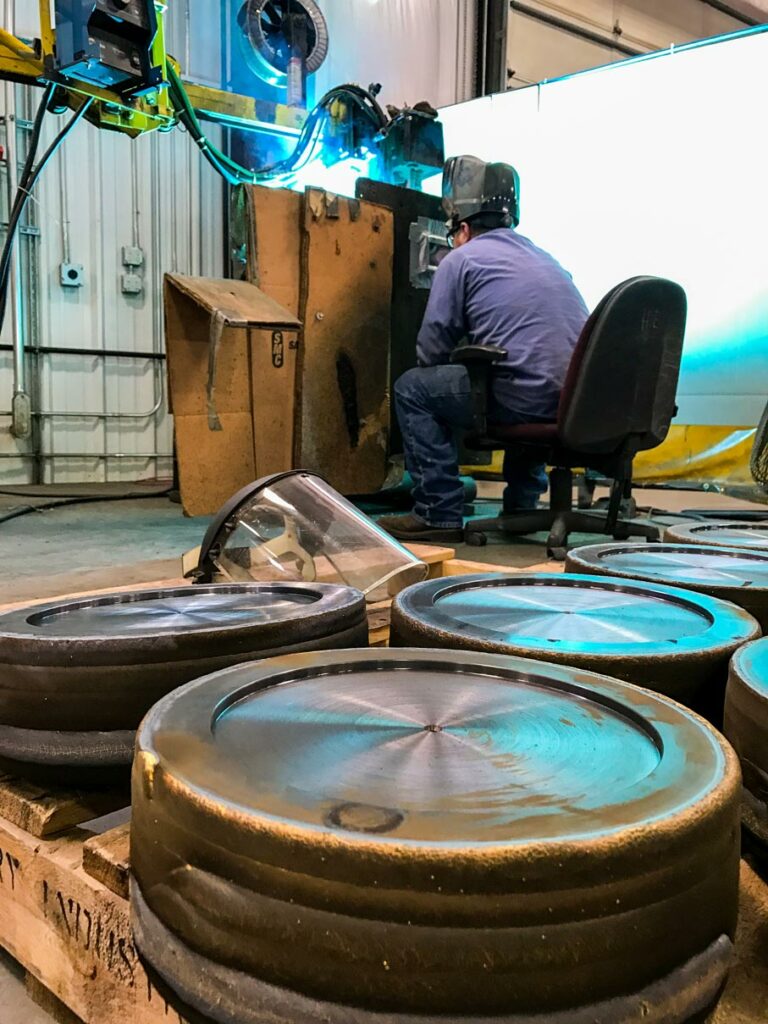
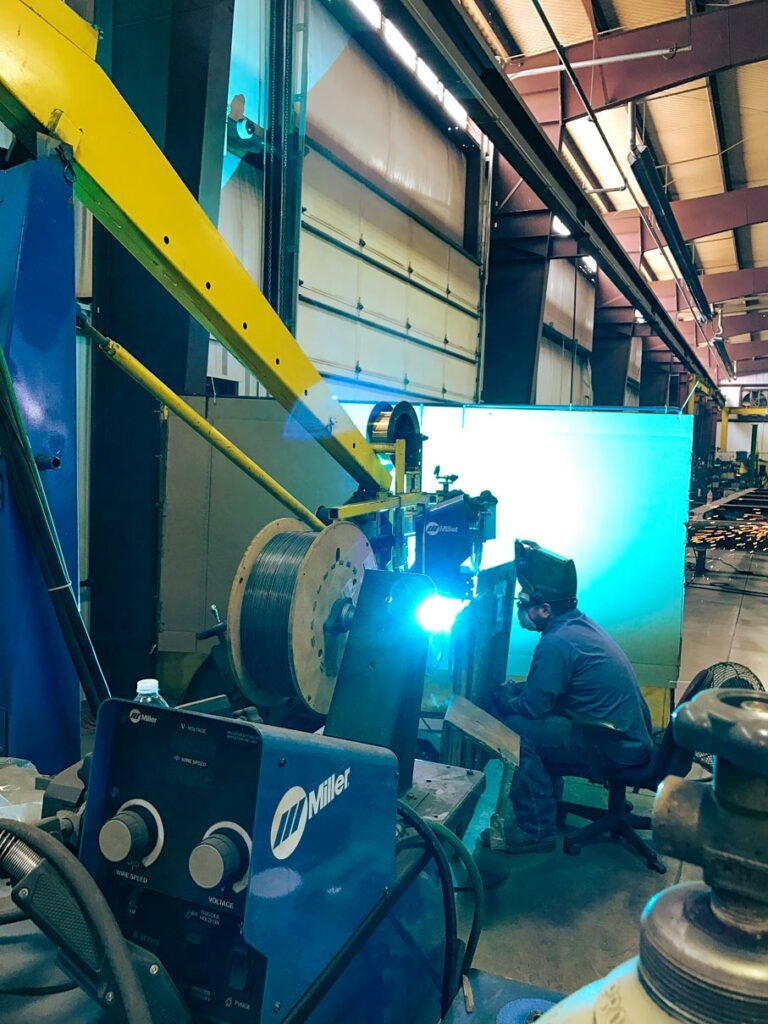
Aluminum Bronze Overlay
The Basic Weld Overlay Procedure:
Surface Preparation – The substrate surface must be thoroughly cleaned to remove any contaminants, oxides, or scale. This ensures proper fusion between the base material and overlay.
Material Selection – We choose the overlay material based on the environmental conditions and performance requirements. Matching the thermal expansion coefficients of the base and overlay materials helps prevent cracking.
Welding Parameters – We then set all of the proper welding parameters, such as current, voltage, and travel speed, to achieve optimal deposition and fusion between the base material and overlay.
Overlay Application – Our expert fabricators carefully weld the overlay material onto the substrate in a controlled manner, layer by layer. The thickness of the overlay depends on the specific application and desired properties.
The Main Benefits of Weld Cladding:
Enhanced Resistance to Wear and Corrosion
Weld cladding protects components from abrasion, frictional wear, heat damage, and other common operational damage. Overlay materials can also provide substantially improved resistance to corrosion, protecting against common rust and the various forms of chemical wear common in today’s industrial applications.
Custom, Fully Optimized Material Properties
Weld overlays allow for the customization of material properties based on your specific application requirements. Both the overall mechanical properties of the product and the surface properties can be fully optimized. Cladding can also be used as a cost-effective repair solution for extending the service life of components without the need for complete replacement.
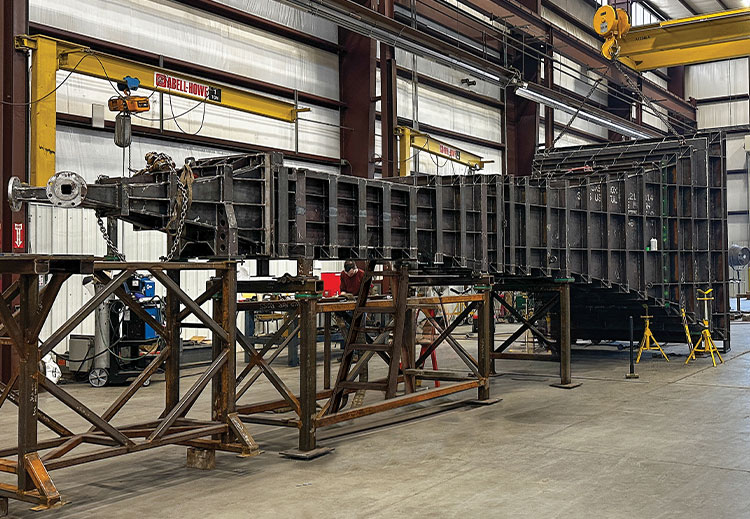
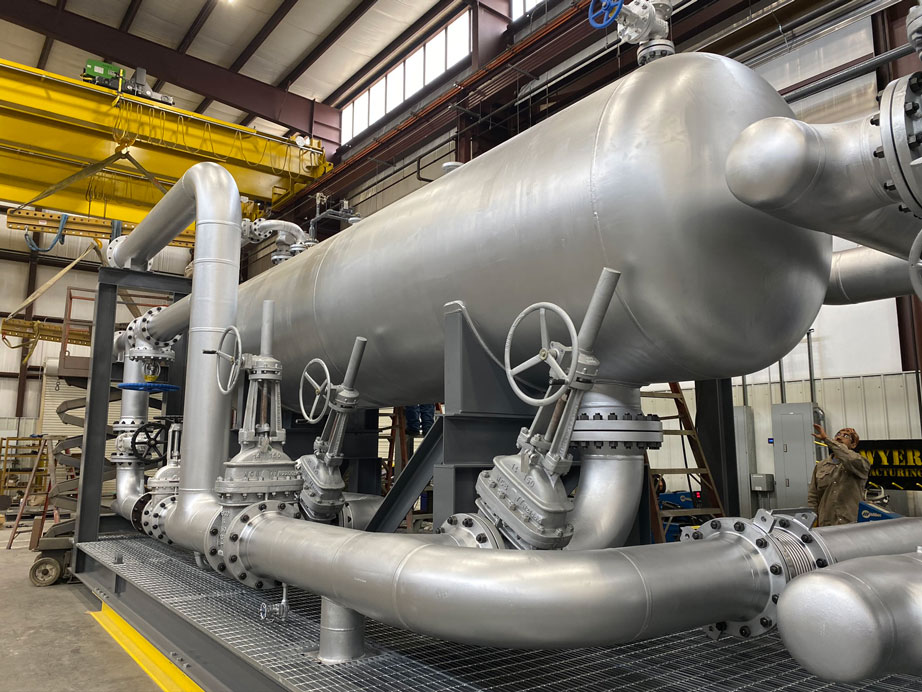

Quality American Welding and Fabrication Services
Based out of Tulsa, Oklahoma since 1948, Sawyer Fabrication has delivered quality American fabrication services for more than 75 years. From the American aerospace sector to the oil and gas industry and beyond, we offer the experience necessary to not only build your products but truly optimize them for the application at hand.
Follow us on Instagram and Facebook to see more of our fabrication and welding projects.