4 Popular Types of Welding Processes Used for Industrial Fabrication
MIG, TIG, Stick, and Flux-Core Welding Services Compared
There are a multitude of different welding processes that are commonly used in the modern fabrication industry. Each type of welding service offers its own unique benefits along with some drawbacks. These advantages and disadvantages will depend upon the type of material required for your project, the target speed/cost of production, as well as the desired quality of the finished welds.
No matter your industry or product application, you can count on Sawyer Fabrication’s AWS certified welding department to deliver the most optimal, quality-focused welding services chosen for your specific project.
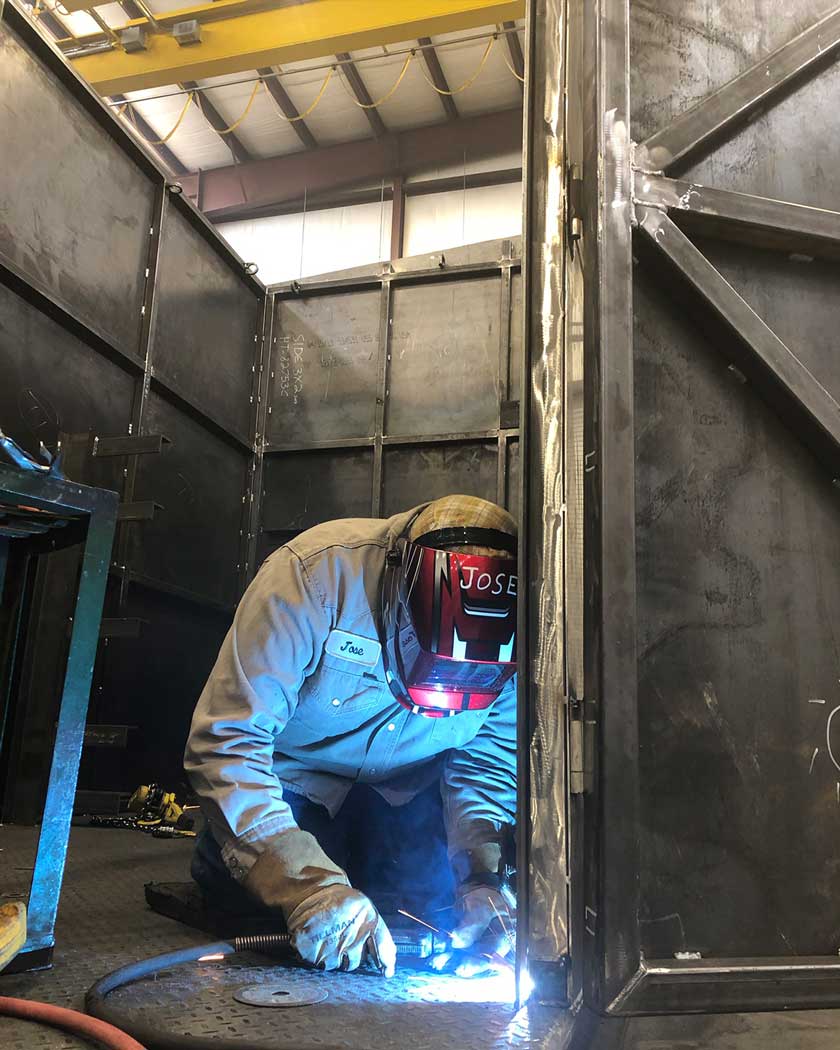
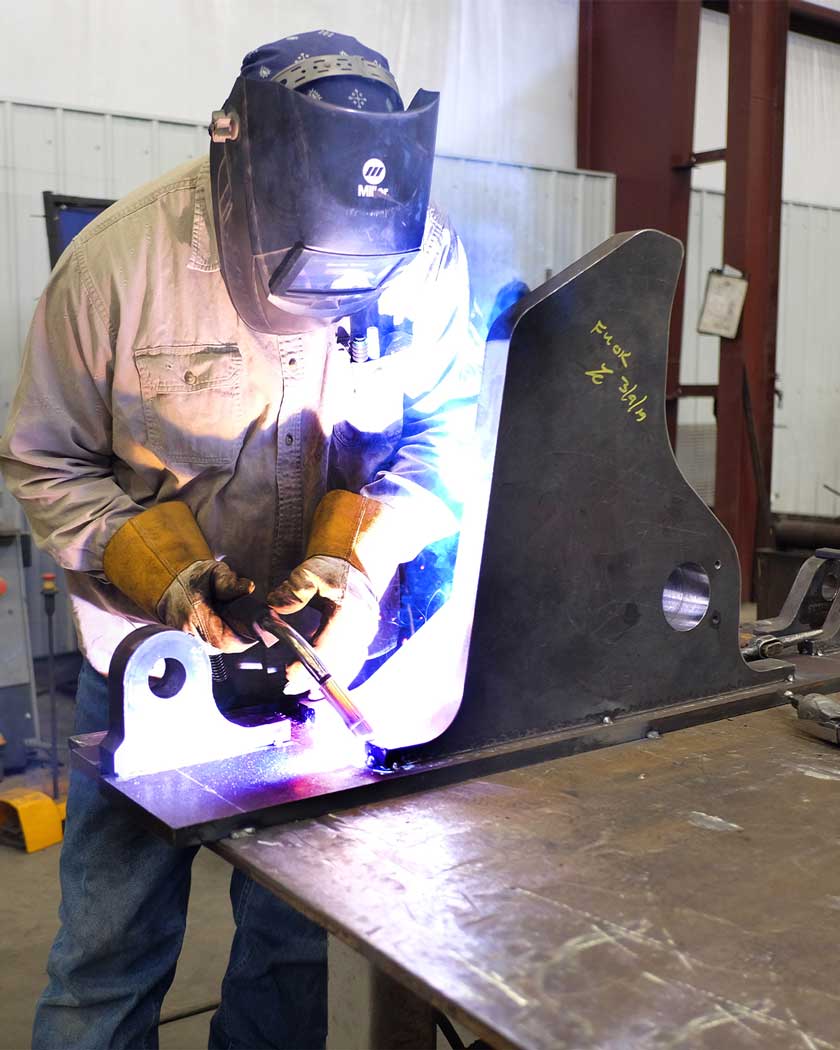
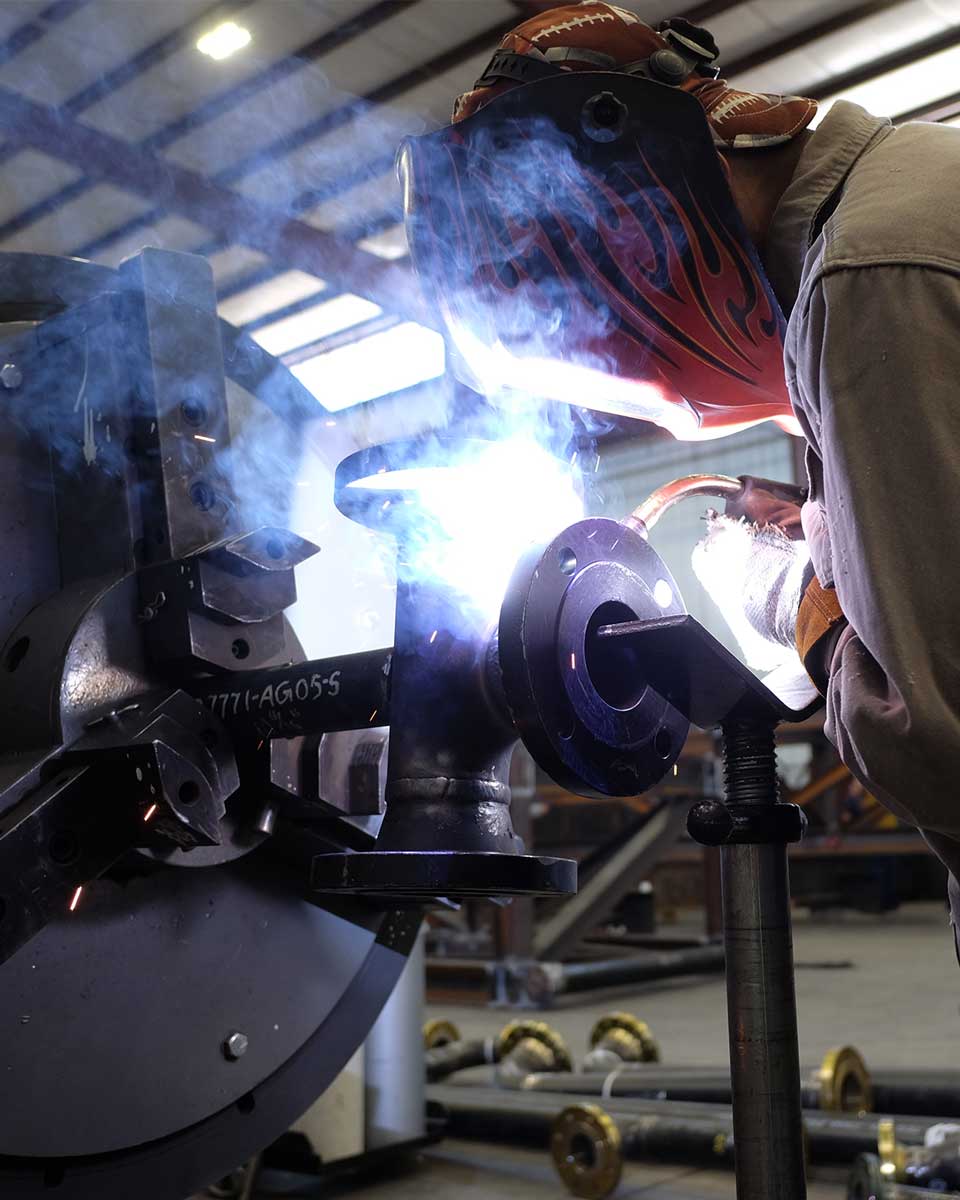
MIG Welding Services
Metal inert gas (MIG) welding is the most common type of arc welding utilized throughout the steel fabrication industry. It is a suitable welding process for thick materials as well as structural welding applications.
Also commonly referred to as gas metal arc welding (GMAW), the MIG welding process uses a consumable wire which melts into the weld’s filler material while simultaneously functioning as the welding electrode.
TIG Welding Services
Tungsten inert gas (TIG) welding is another popular arc welding process used in many commercial and industrial fabrication projects. Commonly referred to as gas tungsten arc welding (GTAW), the TIG welding process uses a hand-fed wire as well as a tungsten electrode, both of which are protected from atmospheric contamination by an inert shielding gas.
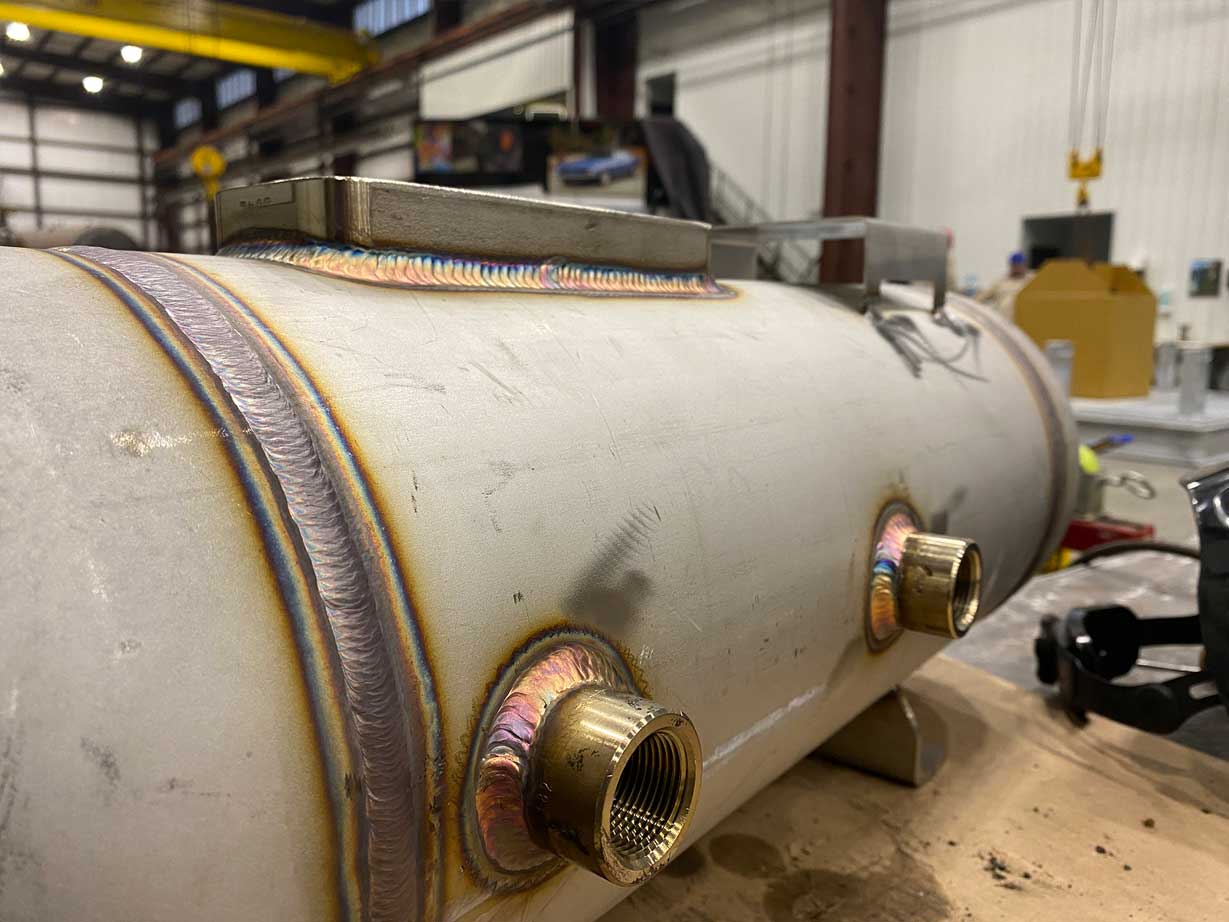
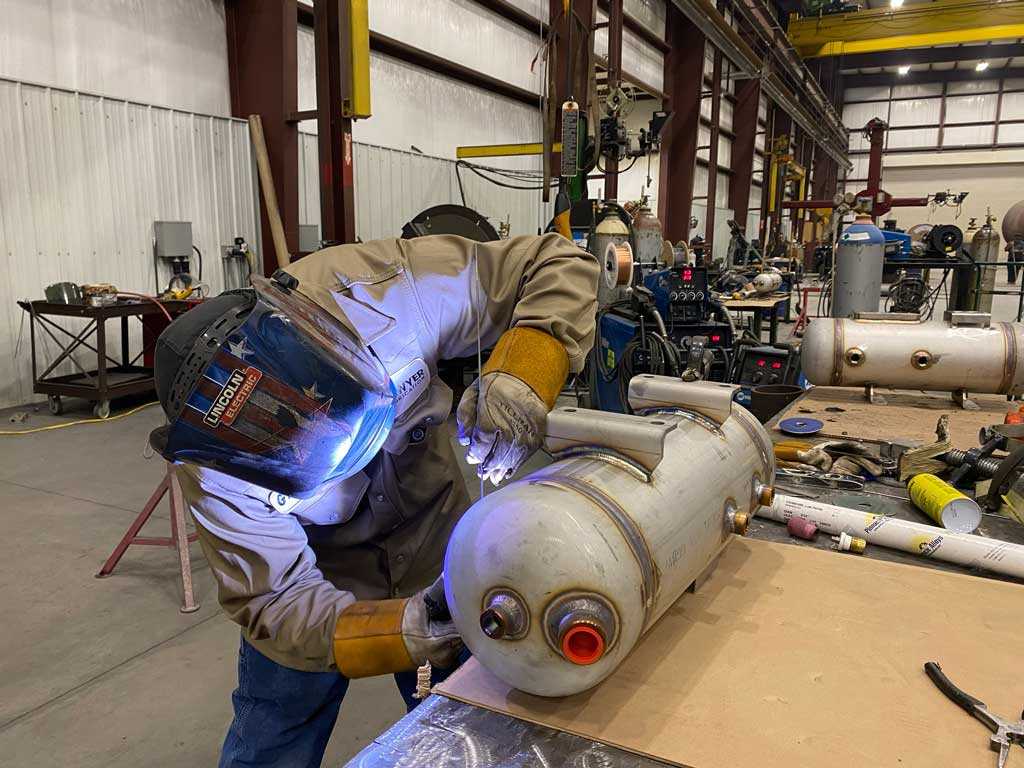
MIG vs. TIG Welding – Advantages and Applications
The TIG welding process is actually slower than MIG welding. However, because the tungsten electrode doesn’t melt into the filler material, TIG welding is more precise and controllable, and offers deeper weld penetration. The GTAW process can also produce more consistent welds that do not require post-production cleanup for aesthetics. Furthermore, the finished welds feature the corrosion-resistant properties of the parent metal.
In contrast, the MIG welding process is simpler and quicker. MIG welding services are easier to perform, and therefore generally lower cost than comparable TIG welding services.
Stick Welding
Stick welding is a relatively simple type of manual arc welding. When a shielding gas is utilized, stick welding can be referred to as shielded metal arc welding (SMAW). However, shielding gas is not required for all applications. The process uses a rod (or stick) electrode which directly creates the welding arc in contact with the workpiece.
Due to the relative simplicity of both the welding process and equipment, stick welding services can be performed more easily and conveniently in indoor and outdoor fabrication projects. Similar to MIG welding, the stick welding process isn’t as precise or clean as TIG welding, so it may not be suitable for some premium industrial product applications.
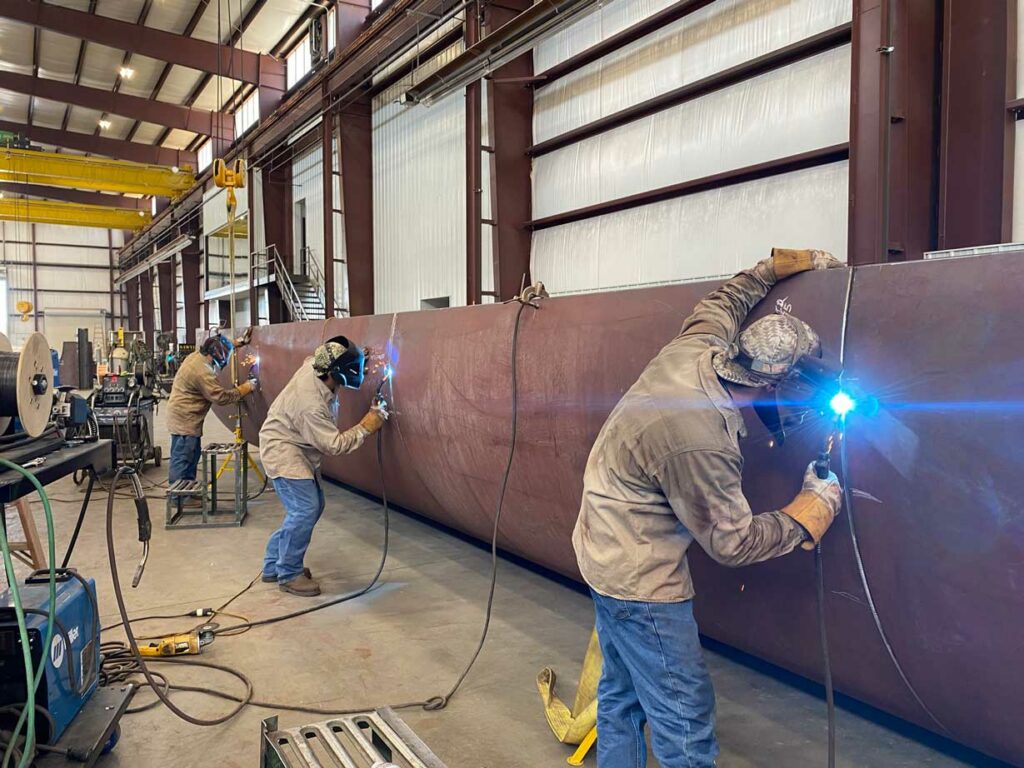
Flux-Core Welding
Commonly referred to as flux-cored arc welding (FCAW), the flux-core process continually feeds a filler wire into the weld pool – similar to the MIG welding process. However, what makes flux-core welding services unique is that a specialized filler wire is used.
As the name suggests, the filler wire is hollow and filled with weld flux. The flux is released as the wire is continuously fed and melted in the weld pool. This shields the weld and protects it from atmospheric contamination, just like in the TIG welding process discussed above. However, unlike TIG welding services, flux-core welding doesn’t require an external gas tank and delivery system, simplifying both the required equipment and production processes.
Quality In-House Welding Services – ASME and NBIC Compliant
Sawyer Fabrication provides complete in-house welding services. Our fully outfitted welding department can provide the most optimal industrial welding process for your specific products and application. We specialize in AWS certified structural welding services as well as ASME certified welding capabilities for pressure vessels and boilers.
Located in Tulsa, Oklahoma, Sawyer offers superior welding and fabrication solutions engineered to meet your most challenging production requirements.